The Future of Manufacturing: Precision Injection Moulding Explained
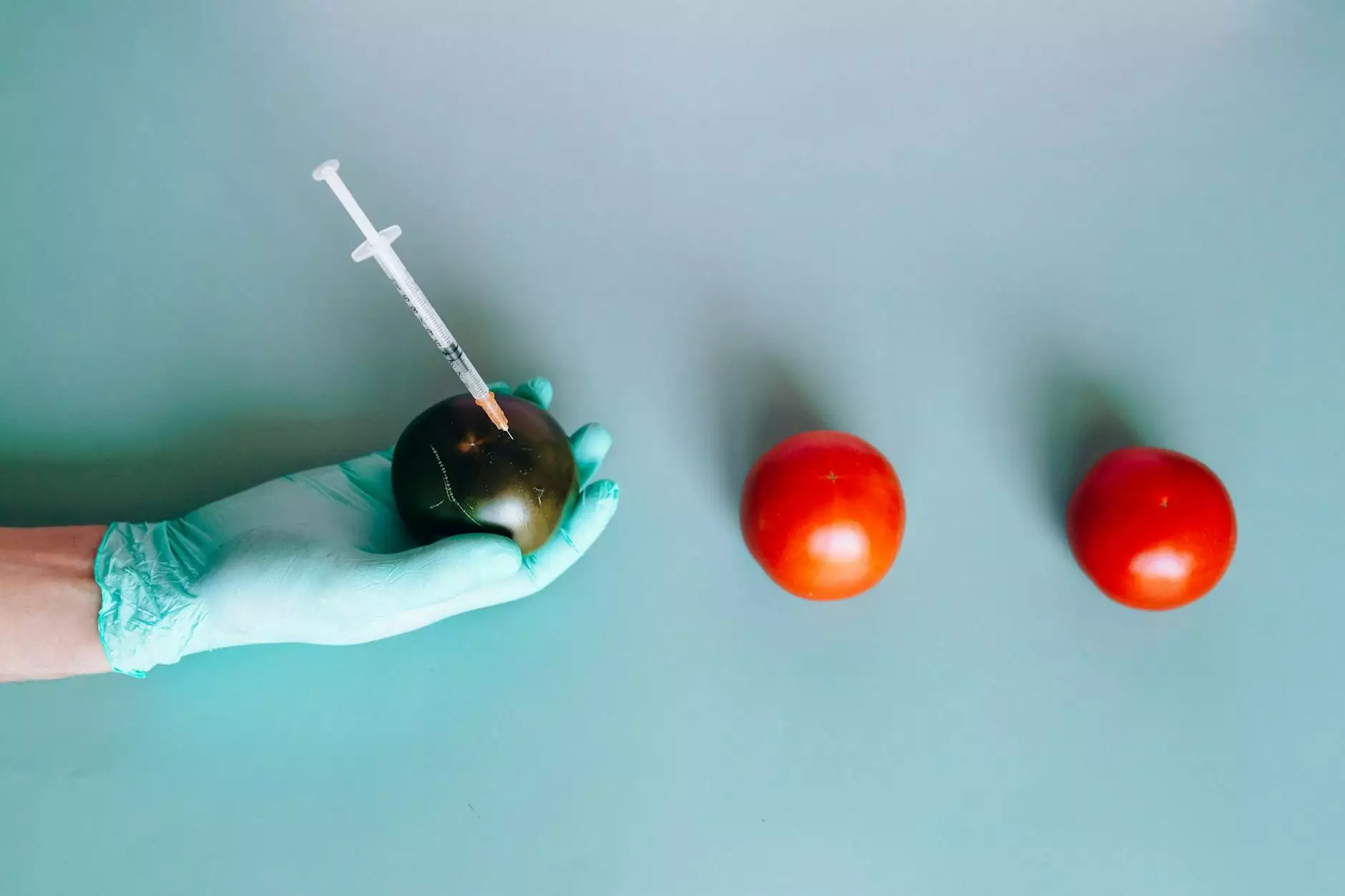
The manufacturing landscape is continuously evolving, and one method that has significantly reshaped production processes is precision injection moulding. This advanced technique allows for the creation of intricate components with unmatched accuracy. In this article, we will delve deep into the various aspects of precision injection moulding, its applications, benefits, and the integral role it plays in industries today, especially within the realm of metal fabricators.
Understanding Precision Injection Moulding
Precision injection moulding is a manufacturing process used to produce parts by injecting materials into a mould. This method is ideal for creating complex shapes with high dimensional accuracy. Often, thermoplastic and thermosetting polymers are used, making it the go-to process for various applications ranging from consumer products to industrial components.
The Process of Precision Injection Moulding
The process of precision injection moulding involves several key steps, including:
- Mould Design: Engineers design the mould based on the specifications of the part required.
- Material Selection: Choosing the right material is crucial, as it will determine the final product's properties.
- Injection: The selected material is heated to a molten state and injected into the mould under high pressure.
- Cooling: Once injected, the material cools and solidifies to take the shape of the mould.
- Ejection: The mould opens, and the part is ejected, ready for any post-processing required.
Key Benefits of Precision Injection Moulding
Understanding the benefits of precision injection moulding can clarify why it is preferred in various industries:
- High Precision: As the name suggests, this method allows for the production of parts with extremely tight tolerances.
- Cost Efficiency: While initial tooling costs can be high, the ability to produce large quantities rapidly reduces the per-unit cost significantly.
- Complex Geometries: It enables the creation of intricate designs that would be difficult or impossible to replicate using other methods.
- Material Versatility: A wide variety of materials can be used, including recycled materials, enhancing sustainability.
- Reduced Waste: The process is highly efficient, minimizing material waste compared to traditional methods.
Applications of Precision Injection Moulding
The applications of precision injection moulding are vast and varied. Here are some industries and products that benefit greatly from this technology:
1. Automotive Industry
The automotive sector utilizes precision injection moulding for creating various components such as:
- Dashboard components
- Housing for electronics
- Fenders and panels
2. Consumer Electronics
Many consumer electronic devices rely on precision moulded parts for:
- Phone housings
- Keypads
- Internal circuit enclosures
3. Medical Devices
In the medical field, precision injection moulding is essential in the production of:
- Surgical instruments
- Drug delivery systems
- Diagnostic equipment
4. Consumer Goods
Household items such as:
- Kitchenware
- Storage containers
- Children's toys
Comparison with Other Moulding Techniques
While precision injection moulding has distinct advantages, it’s important to compare it with other moulding techniques:
1. Blow Moulding
Blow moulding is primarily used for hollow objects, such as bottles. While effective for its purpose, it lacks the precision and ability to create intricate shapes found in injection moulding.
2. Compression Moulding
This technique is better suited for larger, simpler shapes and generally involves longer cycle times. Precision is also less in compression moulding compared to injection moulding.
3. Rotational Moulding
While rotational moulding can create large, hollow objects, it does not offer the precision required for smaller, detailed parts.
Challenges in Precision Injection Moulding
Despite its numerous advantages, precision injection moulding is not devoid of challenges:
- High Initial Costs: Tooling and setup can be expensive, making it less accessible for small-scale productions.
- Material Limitations: Not all materials are suitable for injection moulding, particularly some high-temperature thermoplastics.
- Complex Mould Design: Designing the mould for precision can be a complicated process, requiring expert knowledge.
Future Trends in Precision Injection Moulding
The future of precision injection moulding is bright, with several trends that are likely to impact its evolution:
1. Automation and Industry 4.0
As industries move towards Industry 4.0, automation in injection moulding production is increasing. This includes the use of:
- Robotics for handling parts
- Advanced sensors to monitor temperatures and pressures
- Data analytics to predict maintenance needs and optimize production
2. Sustainable Practices
The push towards sustainability is driving innovations such as:
- Recyclable materials for moulding
- Energy-efficient machines to reduce carbon footprints
- Circular design principles through better waste management practices
3. Advances in Material Science
Research in materials is leading to the development of:
- Stronger, lighter composites with enhanced properties
- Biodegradable plastics that address environmental concerns
Conclusion
In conclusion, precision injection moulding is a transformative technology in manufacturing. It offers unparalleled precision, efficiency, and versatility, making it the backbone of many industries today. As businesses like deepmould.net continue to harness the potential of this method, it holds the promise of driving innovation and productivity to new heights. Embracing technologies and trends shaping this field is crucial for companies aiming to stay competitive and sustainable.
Whether you are a part of the automotive industry, consumer electronics, medical devices, or even consumer goods, understanding and leveraging the benefits of precision injection moulding will only enhance your ability to meet market demands and engineer the future of manufacturing.